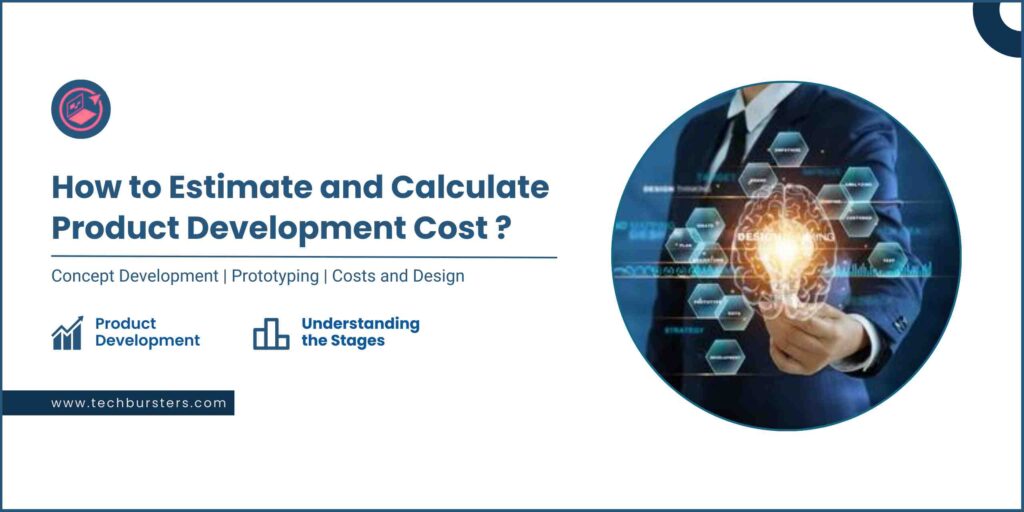
From concept to market, bringing a product forward is an interesting but difficult process with many stages and factors to take into account. Understanding and controlling the expenses associated with this trip is one of the most important ones. Whether your creation is a digital solution or a physical good, several elements affect the total cost.
This blog post analyzes the main elements of product development expenses and offers an understanding of efficient budgeting.
1) Research and Development (R&D) Expenses
The first phase of product development consists of significant research and development. The degree of complexity of the product and the necessary degree of innovation will greatly affect R&D expenses. This period consists of:
Knowing consumer wants, market demand and competitive environment helps one with market research. Surveys, focus groups, and data analysis all fit here.
- Concept Development:
Using feasibility studies and brainstorming sessions, ideas and improvements of product concepts
- Prototyping
Building first models to test and confirm concepts. Simple sketches to advanced 3D models or working prototypes can all fit in here. R&D expenses range from a few thousand dollars for basic products to millions for very sophisticated or novel ideas.
2) Engineering Costs and Design
Digital product engineering comes second once the first idea has been confirmed. This stage guarantees that the product is not only aesthetically appealing but also manufactures sound. Essential elements consist of:
- Industrial Design: Ensuring the product appeals to target consumers by means of its look and feel.
- Mechanical/electrical engineering develops interior systems and components.
- Products needing complex technologies or sophisticated components may find this especially expensive.
- Software Development: Coding, testing, and debugging digital products or those needing embedded software
- Design and engineering costs can vary. For a basic consumer good, expenses may go from $10,000 to $50,000. More sophisticated products—especially those involving major software development—can run into hundreds of thousands or more. For example, making products like Candy AI is more expensive than basic products.
3) Manufacturing Expenses and Materials
Particularly with physical goods, material, and manufacturing costs are a big factor. These expenses include:
- Raw materials: The fundamental components required to produce the good. The kind and grade of the used materials determine the expenses.
- Manufacturing Techniques: Molding, machining, or assembly—among other techniques—are utilized in creating the goods.
- Labor expenses, manufacturing volume, and manufacturing process complexity significantly influence artificial intelligence cost estimation determination.
- Making molds, dies, and other equipment required for manufacturing calls for tooling and setup. Usually, one-time expenses might be rather expensive for complicated products.
- Materials and manufacturing costs are quite flexible. A basic plastic toy might cost a few dollars for each unit to manufacture, for example, whereas a high-tech electronic gizmo could cost hundreds or even thousands of dollars apiece.
4) Certification and Test Fees
Crucially it ensures the product satisfies safety, quality, and legal requirements. Costs of testing and certification consist in:
- Prototypical testing is a thorough investigation of prototypes to find and correct problems.
- Compliance Testing: Verifying the good satisfies industry norms and laws. Safety tests, electromagnetic compatibility tests, and environmental effect analyses can all fit here.
- Certification Fees: Expenses related to acquiring CE marking, UL certification, or FCC approval among other required certificates.
- Depending on the product and the required number of certifications, testing, and certification can cost anywhere from a few thousand to tens of thousands of dollars.
5) Distribution Cost and Packaging
The goods must be packed and sent to consumers after it is produced. Among these expenses are those related to packaging design and materials, thereby producing appealing and protective covering. Simple boxes to sophisticated, branded packaging solutions can all fit under this spectrum.
- Logistics: transportation and warehouse costs; shipping and handling expenses. The weight and size of the goods as well as the distances involved determine the costs.
- Inventory Management: Personnel expenses and warehouse fees among other expenditures related to maintaining and organizing goods.
- Projected expenses for packaging and distribution range greatly. While larger, heavier, or more complicated things could face significant charges, simple items could have less cost.
6) Sales and Marketing Expenses
Bringing a good to market calls for a strong sales and marketing plan. Developing and implementing marketing plans, including internet advertising, social media campaigns, content marketing, and public relations initiatives, these expenses comprise:
- Sales Channels: Direct sales, physical storefronts, or internet platforms all have expenses related to product sales. This covers promotions, listing costs, and commissions.
- Customer Support: Answering questions, addressing concerns, and managing returns.
- Sales and marketing expenses are somewhat varied. While thorough, multi-channel efforts can often run into the hundreds of thousands, a lean marketing campaign could only run a few thousand dollars.
7) Miscellaneous and Overhead Spending
Apart from the direct expenses of creating a product, one needs to take into account certain overhead and auxiliary charges:
- Office rent, utilities, insurance, and other broad corporate costs comprise administrative expenses.
- Legal fees cover additional legal services as well as intellectual property protection including trademarks and patents.
- Miscellaneous Expenses: Unanticipated design modifications, travel, or extra research all fall under unforeseen expenses that could strike throughout the development process.
- Projected expenses are Often accounting for 20–30% of the whole project budget, overhead and other expenses can be somewhat significant.
Result
The intricacy of a good, the materials utilized, and the manufacturing techniques used will all affect its cost. Understanding and considering the several elements of product development costs—research and development, design and engineering, materials and manufacturing, testing and certification, packaging and distribution, marketing and sales, and overhead expenses will help you to build a reasonable budget and properly manage your resources.
Seeking outside money—such as venture capital, grants, or loans—to cover start-up and small business expenses is usually wise. Furthermore, helping to control costs without sacrificing quality includes implementing lean development techniques, open-source technologies, and cost-cutting tactics like outsourcing some activities.
Bringing a good product to market ultimately depends on careful planning and smart budget management. Being aware of the possible expenses and ready yourself will help you negotiate the complexity of product development and position your product for success.
Related Post
- The Best Social Networking App Development Company in India
- Top 10 Game Development Companies in the USA
- Top Software and IT Companies in Chennai